对于大涵道比商用航空发动机,最前端的风扇叶片是尤为重要的,它不仅提供了80%的推力,同时作为航空发动机中尺寸最大的转动零件,其可靠性是影响发动机安全性的关键环节。与风扇叶片相关的气动设计、噪声设计、结构完整性设计等相关技术发展十分迅速,在实际工程设计中更需考虑多场景、不同功能需求,在多专业间权衡,开展风扇叶片的集成设计。
航空发动机已从机械产品时代进入到了功能产品时代,安全、可靠是基本要求,好用、经济则是更高要求。风扇叶片作为影响满足航空发动机推力功能实现的主要零件,同时也作为最大尺寸的旋转件,其功能设计和安全性、可靠性等非功能设计尤为重要。通过了解和分析国内外目前在役发动机的风扇叶片技术现状,理解风扇叶片集成设计,以支撑航空发动机作为功能产品的设计。
风扇叶片技术的重要性
商用航空发动机作为产品,主要服务对象为飞机,最为重要的功能需求是提供推力。因此在发动机气动热力设计中,最基本的设计目标是满足飞机的推力。
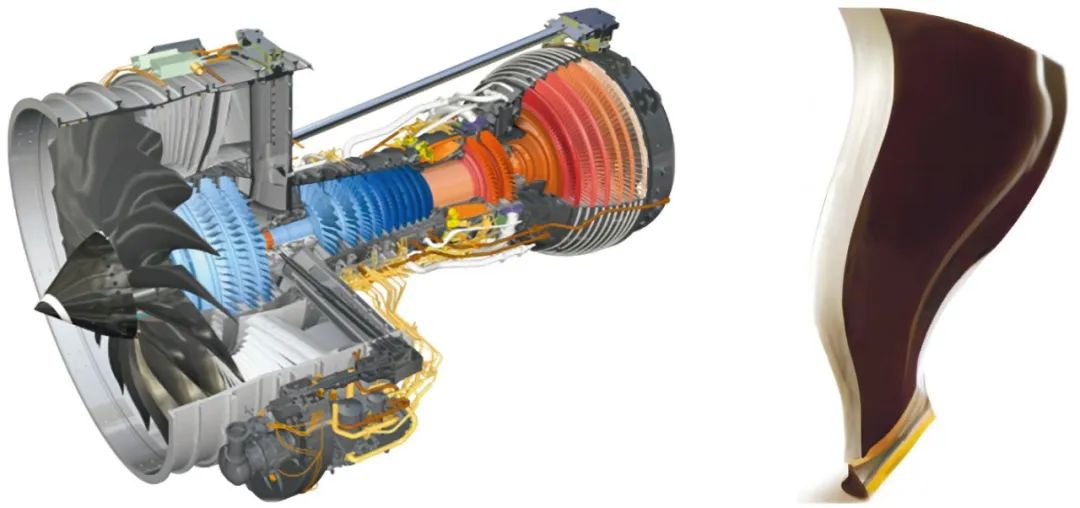
大涵道比涡扇发动机风扇叶片
位于发动机最前端的风扇叶片提供了约80%的推力,因此通常在发动机的控制中会根据风扇特性确定所需推力对应的低压转子换算转速,从而决定增压级、低压涡轮的工作线;根据高低压转子转速的匹配来决定高压转子的换算转速。除此之外,风扇根部的流场品质基本决定了进入发动机内涵道,特别是高压压气机的进气品质;而风扇前端的进气环境受飞行迎角、侧风、结冰等因素的影响,无法人为控制。因此,风扇叶片根部的流场设计和低敏感性设计对于核心机的稳定工作影响极大。与此同时,风扇叶片作为发动机中尺寸最大的旋转部件,是影响发动机可靠性、安全性的关键零件。风扇叶片丢失载荷决定了传力路径上零组件的最低要求,影响风扇叶片结构完整性的各种使用限制也将影响发动机的可操作性。从某种意义上,发动机的各个零件都是服务于风扇叶片,同时也受制于风扇叶片。
从适航条款与风扇叶片的关系也可以看出其重要性。在适航条款中,大部分条款均与风扇有直接或者间接的相关性,如33.65“喘振和失速特性”、33.68“进气系统的结冰”、33.76“吸鸟”、33.77“吸冰”、33.83“振动”、33.94“叶片包容性和转子不平衡试验”等。这些条款既包含对发动机结构完整性的要求,也包含特殊场景、恶劣天气下发动机的操作性、安全性要求。因此,大涵道比航空发动机风扇叶片研发中需综合考虑上述这些条款的约束。
大涵道比涡扇发动机风扇叶片技术的水平,从一定程度上是可以代表大涵道比涡扇发动机的水平。发动机业界一直以来十分重视风扇叶片技术的研究,其发展也是十分显著的。
从风扇叶片气动设计技术的发展来看,三维复合弯掠的气动造型、前缘椭圆造型、为降低前传噪声的后掠叶型设计等,都在考虑气动性能的基础上,更多地考虑了噪声、制造分散性等综合因素的影响。但是随着航空发动机的发展,针对风扇外涵道的效率要求越来越高,已接近0.94;随着对推力需求的增加,涵道比越来越大,已接近15;通过传动技术的提升,风扇叶片叶尖切线速度逐渐下降以适应低噪声、高效率、高可靠性等需求。而叶片数也随着气动设计技术、先进材料等应用,已降至了16片。
风扇叶片高可靠性和轻量化设计也一直在推进之中。因风扇叶片轻量化设计所带来的整个发动机降载收益十分可观,“叶片每降低1kg,发动机降低2.5kg”的说法是有实例为证的。特别是近几十年来的树脂基复合材料风扇叶片的应用,使风扇叶片的轻量化设计有了质的变化,并由此带来了复合材料风扇机匣、流道板等的应用。同时,复合材料具有对缺陷不敏感这一显著不同于传统钛合金风扇叶片的优势。据不完全统计,航线运营的GE90发动机的风扇叶片在十几年内因自身原因仅更换了3片。
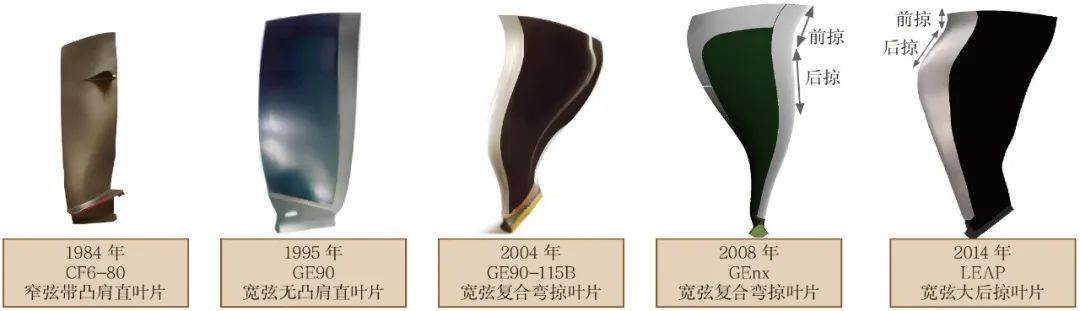
大涵道比涡扇发动机风扇叶片的气动设计演变
风扇叶片技术的复杂性
商用航空发动机产品所采用的技术包含气动、热力、结构、强度、材料和工艺等专业方向最先进水平,同时多专业的匹配性和权衡体现了复杂系统管理工程最高水平,不受人为控制的外界环境变化更是对发动机产品性能的评估和维护水平提出了最高要求。国际上公认航空发动机是一个国家综合工业水平的实力体现,风扇叶片作为这一复杂系统的重要零件,其技术的复杂性尤为突出。
以风扇叶片所处的气动环境为例,从气动设计专业讲,针对已知的进出口条件的气动设计、均匀性设计是传统气动设计的基础,针对稳态设计点的设计方法工具已经极为成熟。但是处于发动机最前缘的风扇叶片进口条件更为复杂,无法直接运用成熟方法工具。
影响风扇叶片气动设计以及风扇叶片气动设计需要考虑的因素,至少包括以下几个方面。
一是进出口畸变的影响。随着短舱技术的不断发展,以及受来自飞机方需求的影响,发动机唇口越来越短,进口流场的品质设计技术也越来越难,此外还需要面临自然环境风、侧风、飞发匹配等影响。在进气畸变场景下稳定工作是风扇叶片气动设计的难题,而更为突出的是在畸变场景下的叶片振动问题。
二是结构完整性的约束。风扇叶片在气动设计之初必须考虑抗鸟撞、抗冰撞等适航要求。外物吸入后叶片损伤、振动带来的气动扰动,也会影响内外涵道的流场品质,从而引起发动机稳定性问题。
三是低敏感性设计。在风扇机匣上风扇叶片叶尖对应区域往往设计有易磨环,用于起飞、降落,甚至鸟撞等场景的叶尖刮磨,在实际使用期间很难保障完美气动流道。同时当遭受鸟撞、冰撞等损伤后,仍然保证推力下降不超过适航或者飞机方需求限制,使得风扇叶片气动设计不仅具有足够的裕度,同时要具有足够的鲁棒性。
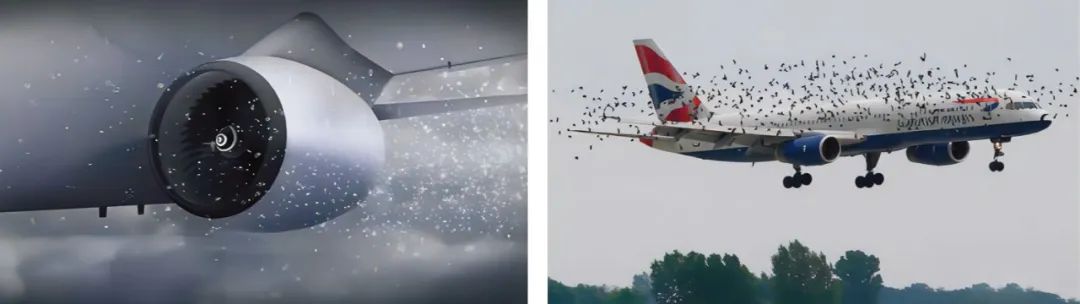
吸冰、吸鸟等外物吸入场景
除了风扇叶片气动设计之外,风扇叶片结构完整性设计更是综合所有可控的和不可控的场景。在结构完整性设计中,需要考虑本身的特性和所处的环境对其的影响。风扇叶片所处的环境极为复杂,除了安装、气动环境外,还受限于整机环境,因为环境所提供的静载荷、动载荷、冲击载荷等,会诱发风扇叶片共振、颤振,以及风扇叶片与机匣刮磨、耦合振动等问题。同时风扇叶片作为转子件,其自身的特性也会对相邻零件产生影响,如风扇叶片安装带来的转子不平衡量问题等。因此,风扇叶片在研发过程中,集成、权衡设计的水平将直接影响发动机的稳定性和安全性。
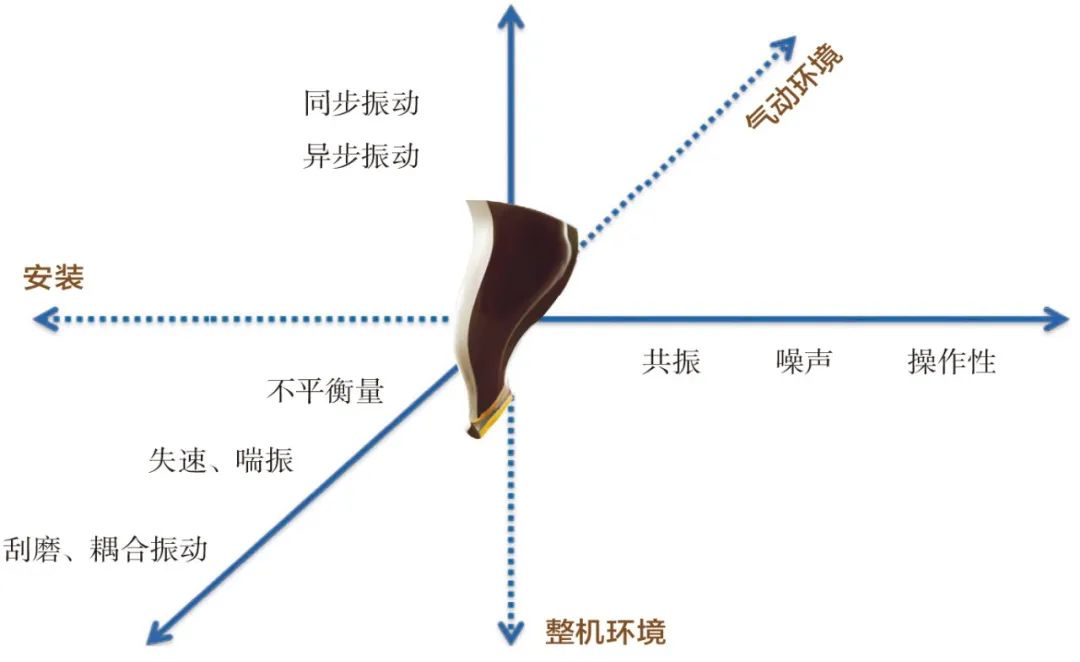
风扇叶片的结构完整性
复合材料风扇叶片技术
在役的新一代大涵道比涡扇发动机大多数采用了复合材料风扇叶片方案。预浸料成型和机织树脂传递模塑成型(RTM)工艺是目前在服役商用大涵道比涡扇发动机复合材料风扇叶片两大主流方案。机织叶片抗分层能力优于铺层叶片,而铺层叶片的可设计性优于机织叶片。采用预浸料成型复合材料风扇叶片的典型是GE90发动机、GEnx发动机以及最新一代GE9X发动机。叶片由数百层增韧环氧/碳纤维预浸带制成,压力面和吸力面都涂有聚氨酯涂层,在叶片前缘增加了钛合金加强边,叶片根部的三角形榫头承受压力的面涂有低摩擦因数的耐磨材料。LEAP发动机则采用2.5D机织RTM工艺的复合材料风扇叶片。
相较于钛合金技术风扇叶片,复合材料风扇叶片的应用具有显著的轻量收益。同时得益于复合材料构件的特点,叶片具有良好的可设计性。另外,可设计性也带来了设计的复杂性,从微观的纤维、树脂到界面性能,延伸到带有铺层或机织结构特征的细观结构性能,最后符合风扇叶片产品功能和非功能需求的宏观性能。
为此,针对复合材料风扇叶片的特点,各国适航当局也公开发布一些专用条件,如1995年发布的针对GE90复合材料风扇叶片的专用条件,内容中主要包含了:针对流道线处的叶片脱落要求;两倍离心载荷的静强度要求;考虑高低周组合影响的叶片流道线以下的寿命评估;叶片流道线以下失效概率的要求;风扇叶片抗雷击能力的要求;需要考虑最小材料性能的要求。
综合分析,针对复合材料应用于发动机叶片,需考虑其不同于金属材料的复合材料特性,以及特别考虑复合材料风扇叶片失效对如风扇机匣等相邻零件的影响。针对不同的复合材料风扇叶片特性,基于特定的发动机型号,保障复合材料风扇叶片具有发动机适航条款要求的同等安全水平,要求具有共同性,同时在不断地完善。例如,针对复合材料风扇叶片,在新近专用条件中提出了止裂特性的验证要求。
除了在役典型的带金属加强边复合材料风扇叶片外,为发挥复合材料可设计性的优势,在已公开的专利中发布了大量特殊设计的复合材料风扇叶片,如外部金属蒙皮,内部复合材料结构特征,并在叶片吸力面施加预应力呈绷紧状态。通过掺入增韧纤维使叶片内部出现瓦伦梁结构等。
目前针对复合材料构建的商用分析制造软件已较为成熟,如针对铺层设计的Fibersim模块,用于强度分析的Hyperworks等。同时,结合LS-Dyna、Ansys等商用软件可以进行风扇叶片强度设计、振动分析和抗外物吸入分析等。
风扇叶片验证技术及保护措施
作为一项航空产品,航空发动机配套有明确的使用说明手册。为指导发动机的正常、安全使用,需要航空公司、飞行员了解所用特定型号发动机的系统特性、使用边界。同时航空公司的飞行计划、飞行员的飞行习惯也会影响航空发动机系统特性的变化。在航空发动机的全生命周期的使用都是在大自然环境中,大自然环境的复杂多变、不受控制,需将上述全部因素考虑在风扇叶片的验证中。风扇叶片的验证技术中最为关键的在于如何筛选试验工况以及如何实现试验工况的模拟。
在吸鸟条款中,针对不同吸入鸟弹工况的差异对于发动机的要求也不尽相同,因此,进而分解到风扇叶片的要求并不相同。例如,当发动机吸入单只大鸟,对于发动机的要求是不得导致危害性后果,但不要求具有保持推力或者功率的能力,此要求类似于发生风扇叶片丢失的场景。因此可以推断,针对吸入单只大鸟情况,风扇叶片是允许发生断裂的。另外一个场景,当发动机吸入大型群鸟后,发动机要求能够保持最大额定起飞推力的50%及以上,完成规定的运转程序,不引起发动机停车和危害性后果。由此可以推断,风扇叶片在吸入大型群鸟的场景,应仍能保持基本结构完整性,不应产生影响气动性能发生超过50%以上推力的材料丢失和型面变化。
在吸冰条款中,与吸鸟条款规定了鸟体的质量不同,对于吸入冰撞击风扇叶片的场景,需要通过相关场景分析,进而分析确定吸冰的质量和不同类型冰的影响。根据参考文献,发动机吸入冰可能来自进气道(短舱)的脱冰、机身脱冰、机翼前缘脱冰以及尾翼脱冰等。同时冰的类型还需考虑明冰、霜冰、混合冰等。冰的本构建立和冰片的制作均需考虑上述情况。在考虑外部环境的同时,还需要考虑场景对应的发动机状态。据不完全统计,发动机吸冰事件多发生于爬升、巡航和下降时,还有少部分发生于滑行、起飞、进近和着陆状态。不同发动机工况下,风扇叶片的旋转速度不同,冰片、鸟弹的冲击破坏也不尽相同,因此如何识别最为苛刻的外物吸入场景,进行相应的试验方案制定和设计尤为重要。
通常在风扇叶片取证过程中,针对不同的条款需求需考虑振动疲劳、抗外物冲击能力、抗缺陷损伤能力等相关验证。风扇叶片因尺寸大、切线速度高导致相关的试验工况模拟比较困难。如针对抗外物吸入试验,考虑鸟体和叶片旋转速度的夹角,使得静止态模拟鸟撞冲击需要实现250m/s以上的鸟弹发射速度,远高于传统航空器的鸟撞速度;旋转部件的结冰及脱冰试验验证、云雾条件的模拟,以及在旋转状态的结冰冰型等关键参数的测量。
风扇叶片的大量验证试验既获取了相应设计方案的使用边界,同时为后续发动机的使用维护提供了大量的输入,甚至可能影响发动机的控制系统。
例如,在役发动机中出现过飞行员推动油门杆,但是发动机推力变化不大的情况。究其根本原因,在发动机的控制中存在油门杆空行程设置,以避免在某个低压转子转速范围停留,防止出现风扇叶片颤振风险。通过后期的使用维护方法来确保已发现的风扇叶片使用问题在发动机全生命周期不发生失效,也是一种常用的手段。
风扇叶片验证试验数量大、成本高。在试验安排中,为规避试验风险和降低试验成本,遵循经典的积木式验证试验矩阵,开展大量的材料试验、元件级试验以及系统级试验,最后在整机试验中予以验证。逐层验证,从材料属性到零件特性,从零件特性到系统特性最终支撑发动机产品的特性确认。